Introduction of spiral finned tubes
Spiral finned tubes are a kind of high-efficiency heat transfer element with spiral fins. Its heat transfer area is several to dozens of times that of light tubes. It can enhance heat transfer, reduce flow resistance, and reduce metal consumption, thereby improving the economy and operational reliability of heat exchange equipment. Spiral finned tubes have been widely used in various boilers. Spiral finned tubes can be manufactured by a variety of methods. The finned tubes used in heat exchange equipment such as boilers and pressure vessels mainly have the following manufacturing methods: high-frequency resistance welded spiral finned tubes, brazed spiral finned tubes and integral spiral finned tubes. The manufacturing method, performance evaluation index, application and advantages of integral spiral finned tubes of spiral finned tubes are introduced in detail.
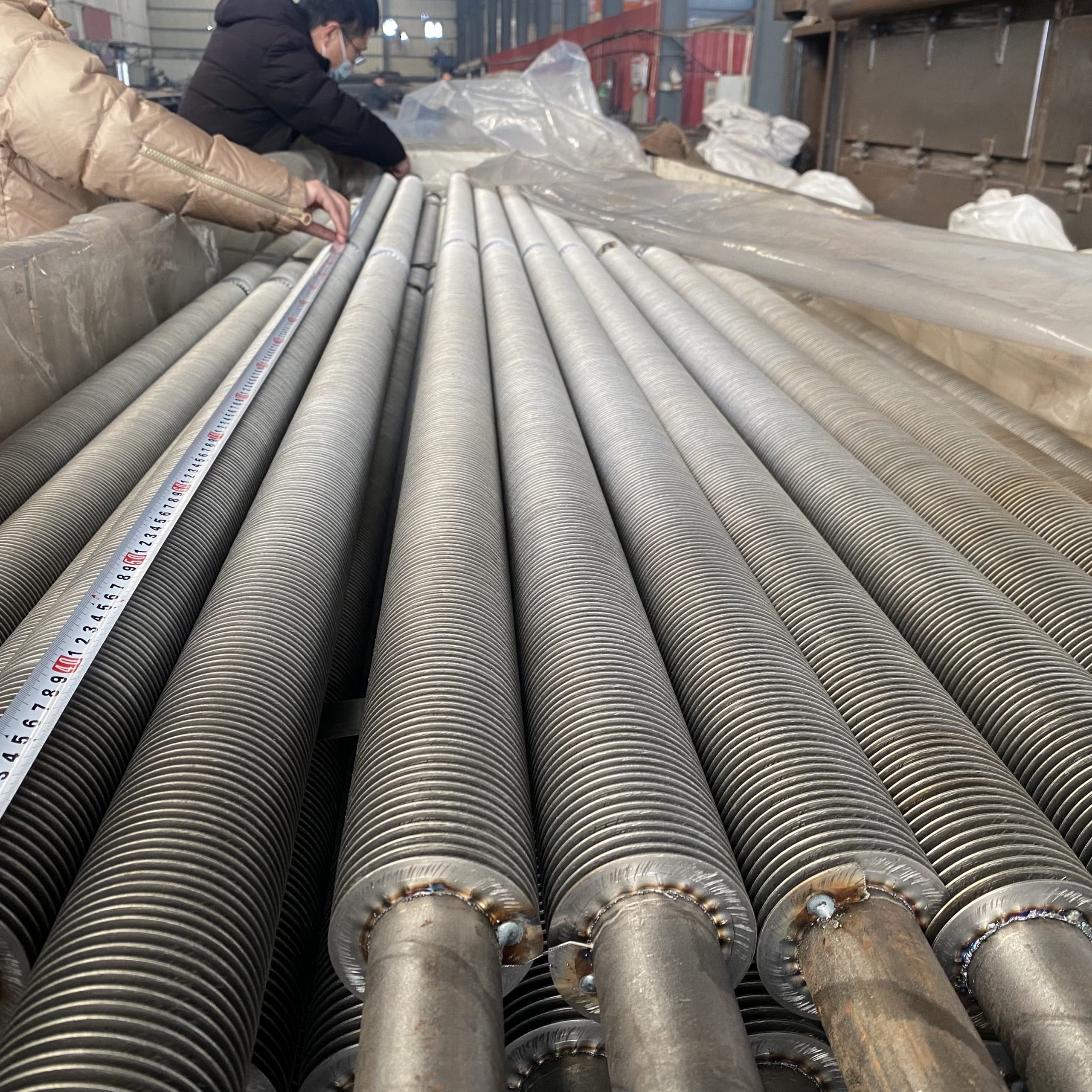
Basic introduction of spiral finned tubes
Spiral finned tubes have been widely used in heat recovery of boiler economizers, air preheaters and waste heat boilers, as well as heat exchange equipment in various fields such as chemical industry and pressure vessels. The unit capacity used in boilers also increases from small to large, and the application is increasing day by day. There are many professional manufacturers in China that can produce high-frequency welding and brazing spiral finned tubes, and the production equipment and technology of finned tubes have been introduced, digested, absorbed, and independently developed, designed, and manufactured, and the quality has reached the requirements of advanced foreign standards.
Advantages of using finned tubes:
1) The heat exchange area is increased in the effective space, improving the heat transfer effect.
2) The space occupied by the heat transfer surface is reduced, making its volume smaller, especially suitable for quick-installed boilers.
3) Reduce equipment costs and improve equipment safety.
4) Due to the reduction of water side pressure drop, the operating cost is reduced.
5) The stiffness of the finned tube is increased, which improves the seismic resistance of the tube.
Manufacturing method of spiral finned tubes
Spiral finned tubes can be manufactured by a variety of methods. The finned tubes used in heat exchange equipment such as boilers and pressure vessels mainly have the following manufacturing methods:
High-frequency resistance welding spiral finned tubes
High-frequency resistance welding spiral finned tubes are to introduce high-power high-frequency current into the welded parts, and use the resistance heat generated by the current passing through the contact surface and adjacent areas of the welded joints to make the welding contact surface reach a molten or semi-molten plastic state, and then apply appropriate pressure to the welding contact surface to complete the welding of the finned tubes.
Brazed spiral finned tubes
Brazed spiral finned tubes are to fill a brazing material with a lower melting point than the welded parts between the welded parts, and then heat the brazing temperature. When the welded parts are not melted, the brazing material melts and wets the brazing, and the brazing joint is formed by diffusion at the contact point of the welded parts, thereby completing the welding of spiral finned tubes.
Integral spiral fin tube
Integral spiral fin tube is a kind of integral spiral fin tube that is formed in one step by squeezing and rolling thick-walled tube (blank tube) under medium frequency continuous heating. It is the latest method of manufacturing fin tube.
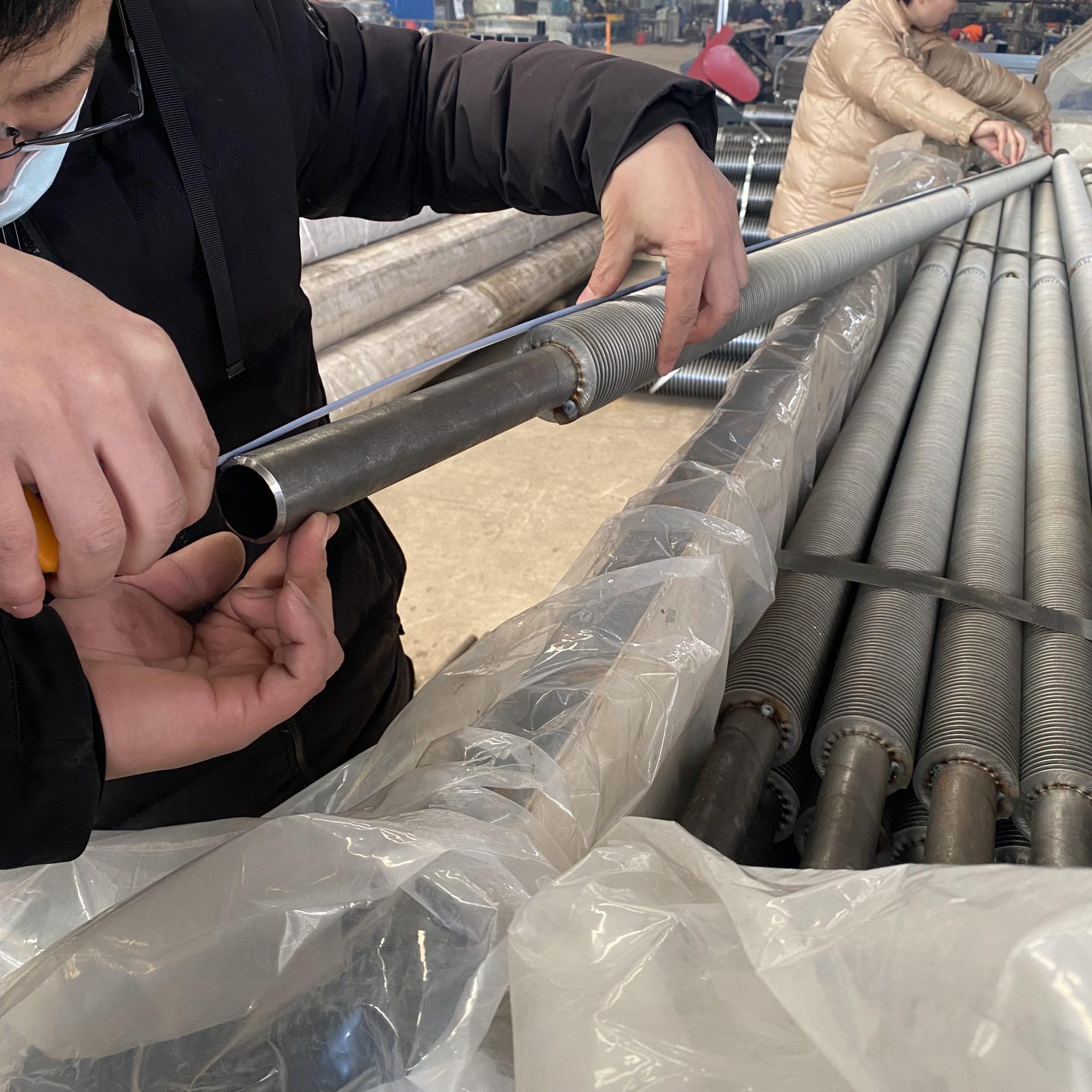
Spiral fin tube performance evaluation index
There are three main manufacturing methods of spiral fin tube. In order to facilitate analysis and comparison, spiral fin tube is divided into welded fin tube (high frequency welding, brazing) and integral spiral fin tube for comparison.
Welding rate, also known as fusion rate.
Welding rate is an evaluation index of fin weld width and total length. JB/T 6512-92 “Technical conditions for manufacturing high frequency resistance welded spiral fin tube for boiler” stipulates: The weld fusion rate in the width direction of the steel strip shall not be less than 80%. Although the length direction is not mentioned, it can be understood that it is qualified if it is not less than 80% along the entire length of the fin.
The length of the local unfused weld shall not be greater than the pipe diameter and not greater than 50mm, and the number of unfused parts shall not exceed 2 per meter, otherwise repair welding shall be performed.
HG/T 3181-1989 “High-frequency resistance welded spiral fin tube” stipulates: The sum of the actual weld length shall not be less than 90% of the total length of the fin, and the average width of the weld shall not be less than 80% of the fin width.
The welding rate of high-frequency resistance welded spiral fin tubes can actually reach 90%-95%, and the welding rate of brazed spiral fin tubes is slightly higher than that of high-frequency welding, but the welding rate is not easy to check.
As the name suggests, the fins of the integral spiral fin tube are generated from the tube, and there is no welding problem of the fins, so there is no need to check the welding rate.
Weld tensile strength
JB/T 6512-92 stipulates: The tensile strength of the welded specimen shall not be less than 196MPa. HG/T 3181-92 does not stipulate this.
For high-frequency resistance welded spiral finned tubes, the manufacturer’s weld tensile strength has reached more than 200MPa, or even more than 300MPa. The weld tensile strength of brazed spiral finned tubes can basically meet this requirement.
The fins of the integral spiral finned tube are extruded and rolled from the billet tube, and there is no problem with the tensile strength of the weld. The strength of the connection between the fin and the tube is equivalent to the tensile strength of the corresponding pipe, or even slightly higher.
Post-weld heat treatment
The weld heat affected zone of high-frequency resistance welded spiral finned tubes is very small. Foreign standards stipulate that the heat affected zone is <<0.8mm, and the actual heat affected zone of some domestic manufacturers’ products is less than 0.5mm. Therefore, some standards do not stipulate whether the high-frequency resistance welded spiral finned tubes should be heat treated after welding. JB/T 6512-92 standard stipulates: Alloy steel finned tubes should be heat treated to eliminate stress after welding.
The production process of the integral spiral finned tube is actually another extrusion and rolling process of the original thick-walled billet tube at high temperature. After extrusion and rolling at high temperature, there is no need for stress relief heat treatment.
Heat transfer effect
The heat transfer effect of high-frequency resistance welding and brazing spiral finned tubes is at least 4 times higher than that of light tubes. The heat transfer effect of toothed finned tubes is better than that of complete fins. However, it should be noted that the welding rate of the weld between the fin and the tube is not 100%, and the standard stipulates that it is only more than 80%. There is thermal resistance in the unfused part, which will affect the heat transfer effect.
The fins of the integral spiral finned tube are 100% in contact with the mother tube, and the small R transition between the root of the fin and the mother tube during molding not only increases the stiffness and pressure bearing capacity of the fin, but also facilitates the transfer of heat. Its heat transfer effect can be at least 5-6 times higher than that of light tubes, which is significantly better than the heat transfer effect of high-frequency resistance welding and brazing spiral finned tubes.
Service life
The welding of high-frequency resistance welded spiral finned tubes is to apply pressure while melting the contact points of the two metal surfaces. The welding rate is good, and the corrosion resistance of the weld metal is more than doubled compared to brazing, which can greatly improve the service life of the finned tube. However, due to the weak welding, long-term use is prone to weld cracking, which causes the fins to separate from the tube, thereby affecting its heat transfer efficiency and requiring the replacement of the finned tube.
The integral spiral finned tube does not have the problem of fin welding, so there is no need to worry about fin corrosion, cracking, etc., and its heat transfer efficiency will not be reduced. Furthermore, due to the increase in the surface hardness of the integral spiral finned tube, the wear resistance of the finned tube is increased, and the structural characteristics of the root of the fin facilitate heat transfer. Therefore, the service life of the integral spiral finned tube is equivalent to the life of the raw material of the finned tube, which is at least 2-3 times the service life of the high-frequency welding and brazing spiral finned tube.
Economical
The brazed spiral finned tube requires a third material-brazing filler metal. During brazing, the fins need to go through the main processes of cold winding, spraying solder, sintering, etc., so the manufacturing cost is relatively high. High-frequency resistance welded spiral finned tubes do not require a third material, and the fins are formed by one-time winding welding, so the cost is relatively low. The starting and ending ends of high-frequency resistance welded and brazed spiral finned tubes should be fixed by manual welding before welding.
The integral spiral finned tube is made of thick-walled tubes through extrusion and rolling. No second material is required, which saves multiple processes in the production process of winding and welding of high-frequency resistance welded fins, with high production efficiency and low cost. In addition, since the root of the fin of the integral spiral finned tube is a small R smooth transition, it is convenient for heat transfer.
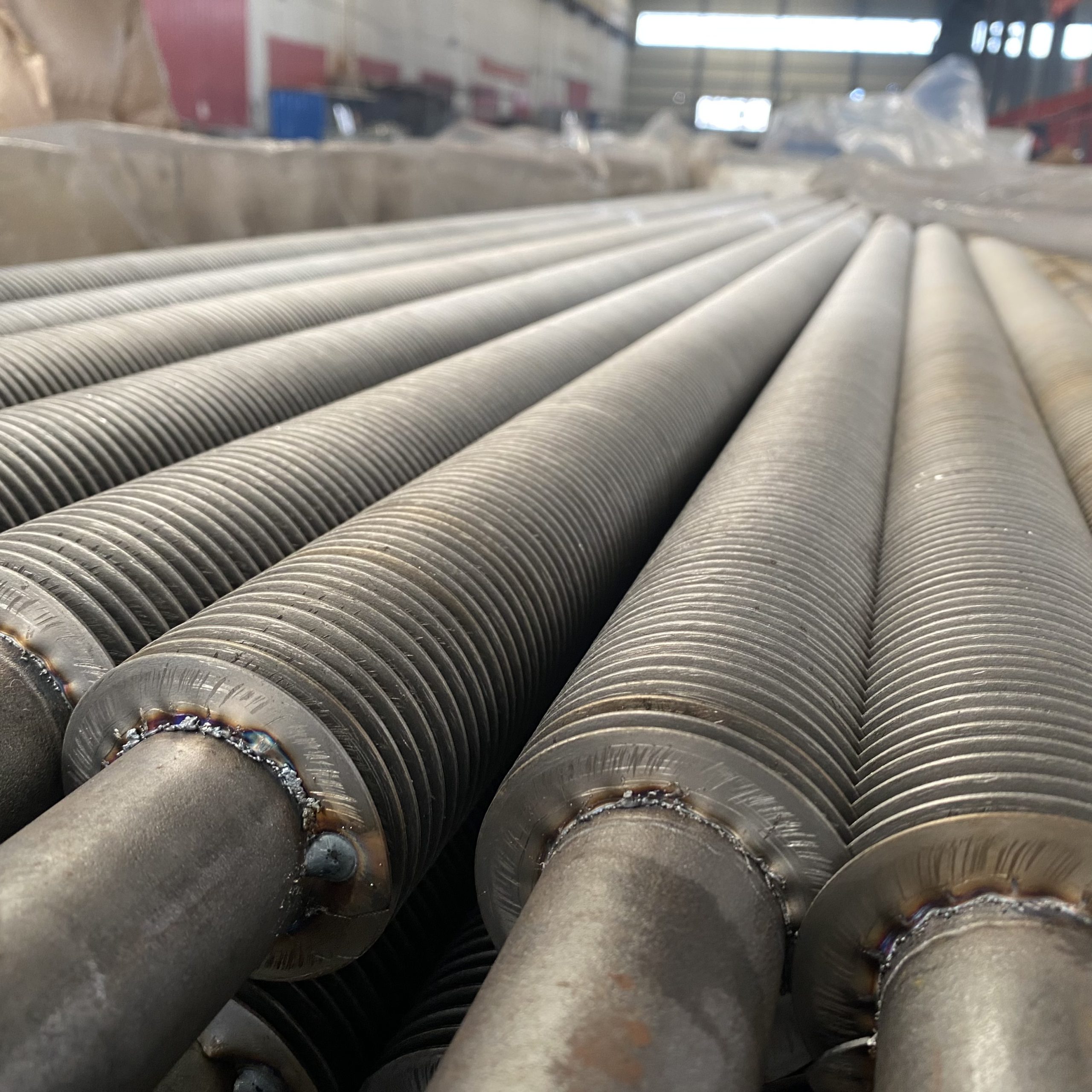
Technical advantages of spiral finned tubes
The spiral finned steel tubes used are mostly winding, high-frequency welded, and brazed spiral finned steel tubes. The integral spiral finned steel tube has a long service life, stable heat transfer performance, and obvious energy-saving effect. It has become a replacement product for the above three types of spiral finned steel tubes. Its advantages are as follows:
- Long service life, which is more than 3 times that of the winding welded finned steel tube.
- The fin root forms an arc cut with the tube, and the fin surface is smooth, which completely eliminates the dust accumulation, ash blockage and slagging phenomenon that is easy to occur in other forms of fin tubes due to the uneven folding of the fin root.
- The hot rolling process is adopted to improve the density, yield strength, tensile strength and wear resistance of the metal structure.
- Since the fins and tubes are an integrated structure and distributed in a spiral band, the pressure bearing capacity of the integral spiral fin steel tube is more than 3 times that of the seamless steel tube with the same wall thickness and inner diameter.
- Wear resistance solves the problem of severe wear of the convection heating surface of coal-fired boilers due to high wind speed and high ash concentration. (Especially circulating fluidized bed boilers)
- The fins and tubes are an integrated structure, which completely eliminates the contact thermal resistance that cannot be overcome by other forms of fin steel tubes due to the two-body structure of the fins and tubes, and the longitudinal section of the fins is a trapezoidal structure, so the heat exchange efficiency of the fins is maximized.
- The integral spiral fins are used to expand the surface heat exchange. Under the same working conditions, the heat transfer coefficient of the tube bundle is 3.5-5.5 times that of the seamless steel pipe with the same wall thickness and inner diameter, and is twice that of the welded spiral fin steel pipe with the same specifications.
- The fins and the tubes are an integrated structure, so they are used in working places with high temperatures and harsh environments. The unstable heat transfer performance caused by the loosening and falling of the fins, which is easy to occur in other forms of finned steel pipes, will not occur.
FAQ
1. Q:I haven’t done business with you so we want to make online order to protect me,is it Ok for you ?
A: Our company has been in filed for 10 years, Your Alibaba online order is welcome, we we will provide good service to you.
2. Q: What is the MOQ? Can I place small order please ?
A: Small order is also welcome in our company.
3. Q: How long warranty can we have for my orders
A: One year warranty for all products, 2 years warranty available for some specific orders.
4 Q: What service can you provide ?
A: We will confirm all details with you before payment, any changes will let you know in advance, any progress will show you photos and video for your reference and will let you know your order’s status. Will send draft documents for your reference before issuing official document.
5, Q, How do you control quality ?
A:Datang produces Fin Tube and Heat Exchangers since 2007 and we passed ISO 9001 in 2007. We are serving hundreds customers whom from 40+countries around the world. All products will be 100% tested before shipping out.
6, Q, What are your main products ?
A: We mainly produce fin tubes,air heat exchangers, surface coolers, evaporator coils, condenser coil, shell and tube heat exchangers, plate heat exchangers and other heat exchange equipment and all kind of finned tubes, heat exchange accessories, etc.