Serrated Finned Tube:
Core tube material: carbon steel, low alloy steel, stainless steel, brass, copper, copper-nickel alloy, aluminum bronze, nickel alloy.
1. Carbon steel: A179, A192, SA210 Gr A1/C, A106 Gr B
2. Stainless steel: TP304/304L, TP316/TP316L
3. Copper: UNS12200/UNS14200/UNS70600, CuNi70/30, CuNi 90/10
4. Titanium: B338 Gr 2
Fin type: U fins,perforated,twist…
Fin material: aluminum, copper, steel
1. Aluminum (Alu.1100, Alu.1060)
2. Copper.
3. Steel
Fin Tube Type: Plain Strips
Fin number: 2/ 4/ 8/ 16/ 18/ 32/ 36 piece per row
Number of fins: 16/20/24/32/40
Tube OD: 19mm min.
Tube Length: 25 meters max.
Fin height: 16.5mm max.
Fin thickness: generally 0.4mm~0.6mm
Fin pitch: 2.1mm minimum (12FPI)
Surface Protection: Both bare ends shall be zinc or aluminum metallized by electrospray arc system coating.
Accessories: Tube support boxes, clamps or spacer boxes (materials: aluminium, zinc and stainless steel).
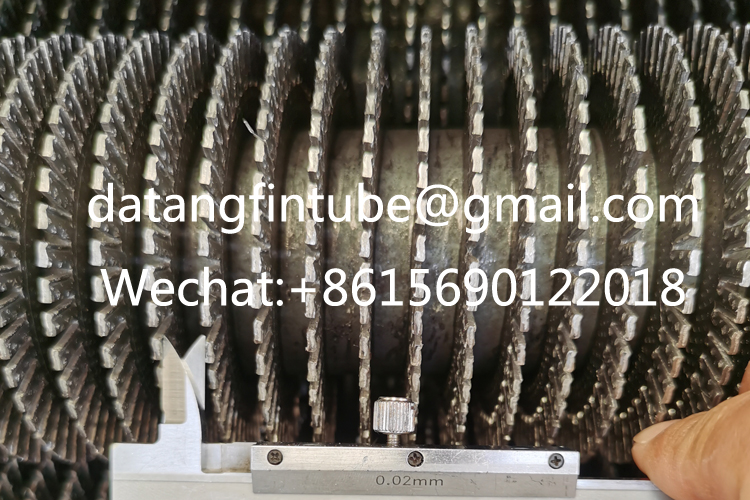
Serrated Finned Tube is combined with two different materials
Core tube material: carbon steel, low alloy steel, stainless steel, brass, copper, copper-nickel alloy, aluminum bronze, nickel alloy.
Carbon Steel Tubes | A179, A192, SA210 Gr A1/C, A106 Gr B, A333 Gr3 Gr6 Gr8, A334 Gr3 Gr6 Gr8, 09CrCuSb, DIN 17175 St35.8 St45.8, EN 10216 P195 P235 P265, GB/T3087 Gr10 Gr20, GB/T5310 20G 20MnG, |
Alloy Steel Tubes | A209 T1 T1a,A213 T2 T5 T9 T11 T12 T22 T91,A335 P2 P5 P9 P11 P12 P22 P91,EN 10216-2 13CrMo4-5 10CrMo9-10 15NiCuMoNb5-6-4 |
Stainless Steel Tubes | TP304/304L, TP316/TP316L TP310/310S TP347/TP347H |
Copper Tubes | UNS12200/UNS14200/UNS70600, CuNi70/30, CuNi 90/10 |
Titanium Tubes | B338 Gr 2 |
The serrated spiral high-frequency welded fin tube is a metal element with high efficiency heat transfer, which is widely used in various industrial fields.
Its structure consists of a base tube and a toothed fin. The fin is welded to the base tube by high-frequency welding technology to form a whole.
The main features of the serrated spiral high-frequency welded fin tube include high heat transfer efficiency, wear resistance, corrosion resistance, and long life.
The heat transfer efficiency of the serrated spiral high-frequency welded fin tube is very high. The fins are serrated, which can effectively increase the contact area between the fins and the air, thereby improving the heat transfer efficiency.

In addition, the fin tube has a compact structure and occupies a small space, which is particularly suitable for application scenarios such as quick-installed boilers that require a compact structure.
This high efficiency heat transfer performance makes fin tubes widely used in various industrial fields, such as chemical industry, pharmaceutical industry, food processing, heating, etc.
The serrated fin tube also has good wear and corrosion resistance.
Fin tubes are usually made of metal materials such as stainless steel, aluminum, copper, etc. These materials have good wear and corrosion resistance, which can effectively extend the service life of fin tubes.
The fin tube is also treated with high-frequency welding, which makes the connection between the fin and the base tube more firm, less prone to loosening or falling off, and further improves the wear resistance and corrosion resistance of the fin tube.
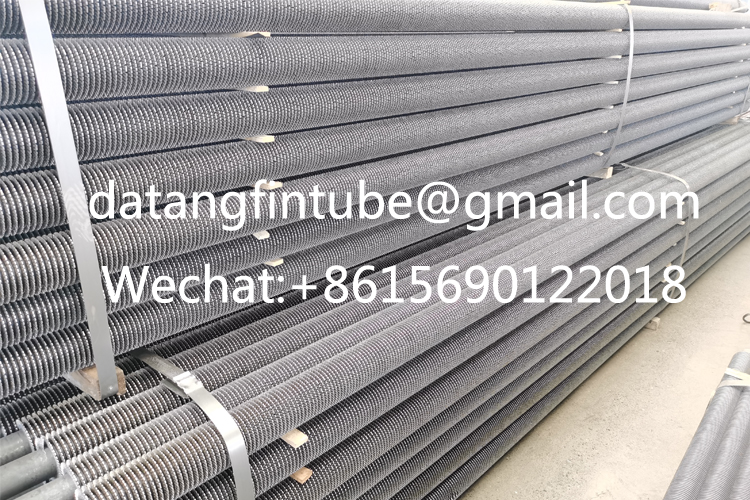
The serrated spiral high-frequency welded fin tube also has certain advantages.
It can effectively increase the heat transfer area, enhance the heat transfer effect, reduce the space occupied by the heat transfer surface, and reduce its volume.
Fin tubes can also reduce equipment costs, enhance equipment safety, and reduce operating costs.
These advantages make fin tubes widely used in various industrial fields and highly praised by users.
There are also some disadvantages of serrated spiral high-frequency welded fin tubes.
Due to process limitations, the fin spacing is large and the fin height is high, resulting in low fin ratio and limited heat exchange effect.
The fin is a steel sheet or stainless steel sheet, the sheet is thicker, the thermal efficiency is poor, and the heat transfer efficiency is low.
These disadvantages limit the application of fin tubes in some special application scenarios to a certain extent.
The serrated spiral high-frequency welded fin tube is a metal element with high efficiency heat transfer and has broad application prospects.
In practical applications, it is necessary to select appropriate materials, processes and structures according to the specific use environment and needs to give full play to the advantages of finned tubes, overcome their disadvantages, and improve heat transfer efficiency and equipment performance.
With the continuous advancement of science and technology and the continuous development of industry, it is believed that finned tubes will be used in more fields and play a more important role.